First let me introduce myself, my name is Andrew Burns and I’m a rocket propulsion engineer and amateur photographer living in Auckland, New Zealand. I’m 33 years old, meaning that I owned and used film cameras when I was a kid (I can remember owning a Pentax Espio, but not which one) but I didn’t really get interested in photography until well after digital had taken over.
In late 2018 I was on a holiday with my partner to Europe and while at a flea market in Hamburg I decided to buy an old film camera because I was bored of looking at old junk. I walked away with a barely working Minolta SRT100 and a 50mm lens but I was really excited to try it out. Two years later and I’ve fallen head-first down the film rabbit-hole and mostly use a Chamonix 4×5 large format camera while the digital camera is relegated to ‘scanning’ film. I’ve always been the kind of person who wants to do everything myself, so naturally I’ve been home-developing from my first roll.
As much as I like the process of hand-developing film and find it quite easy now (even E6), it does get a bit tedious after a while (especially E6), so naturally being an engineer I thought about building a machine to do it for me. I started designing something up in about March of 2019; my initial design looked somewhat like a rice cooker, with the developing tank and chemical bottles sitting in a water bath and the film reels on a vertical shaft like in a Paterson tank.
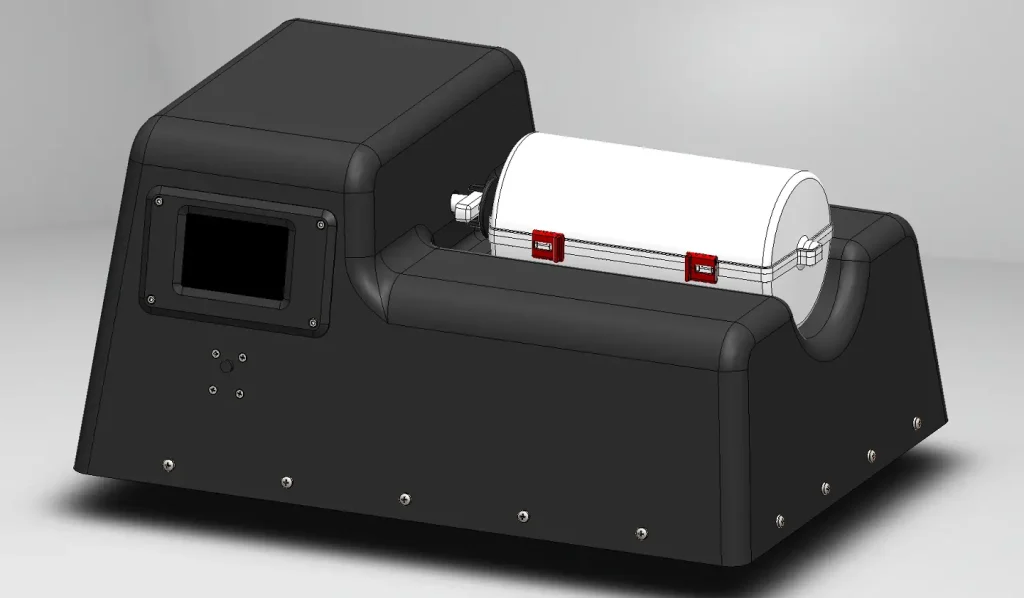
One day by chance I mentioned my idea to the owner of a local film lab who was really interested in something to replace the Phototherm they use for B&W developing. He encouraged me to get in-touch with some other film lab owners to get an idea of what people wanted, so I sent out a survey to a number of people and labs currently using similar small automatic developing machines. Typically it seemed that the people surveyed wanted the following:
- A fully automatic film developing machine with support and spare parts available
- Capable of processing B&W, C41 and E6
- Capable of working with at least 6 different chemicals at a time
- Capable of processing at least 6 rolls of 35mm film at a time
- Reliable and easy to use/program
- Options for using bulk chemicals and replenishment
With these new requirements I had to throw my rice-cooker design in the trash and start again. Vertical developing tanks use too much chemistry, water baths for heating are too slow and limit the number and volumes of chemistry you can work with. For these requirements the optimal design really does start to look more like the venerable Phototherm machine, albeit significantly modernised and designed for production.
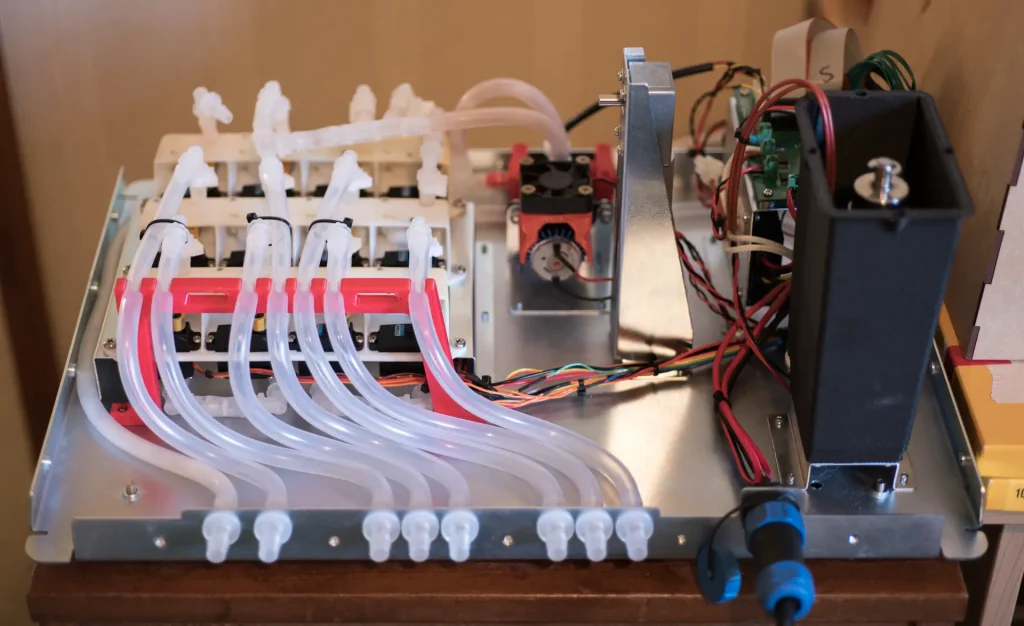
And so started the process that you can follow in significantly more detail on my website, to be honest I have a bit of a habit of biting off more than I can chew and if I’d known how much effort this project would be I might not have started it in the first place. It’s very difficult to design and build a product like this from scratch and because I haven’t begun selling anything yet it’s only me working on this project in my spare time. I have to wear so many different hats, mechanical designer, electrical designer, marketing, procurement, accountant, photographer, website builder, social media etc.
The Chromabox is currently in the testing phase so right now it feels like every day I find a new problem to fix, but this is in some ways the most important phase of design because every issue I find now is one less thing the end-user might encounter. I’m a bit of a perfectionist and the thought that something might go wrong with one of my machines ‘in the wild’ is a bit of a nightmare, almost as bad as if something I designed which is critical to one of the multi-million dollar rockets it’s on might fail. I’m sure the Chromabox is at the point where some people might start to crowd-fund or take pre-orders, but I really want to make sure that what I eventually release is as good as it can be before I take that step.
Most of the issues that I’ve encountered throughout the design and testing of the Chromabox have been practical in nature, things like leaky valves, tanks not draining properly, sensors not detecting when they should, ensuring accurate temperatures etc. Most people don’t realise that the only thing making consumer electronic products like printers or coffee machines so cheap is the vast economy of scale behind them. If you had to make a coffee machine out of off-the-shelf industrial components it would cost $50k and be the size of a bar fridge. I don’t imagine that I’m going to sell enough of my machines to really make fully custom parts work for me, so from the start I’ve tried as much as possible to source components that are used in other applications so that I can piggyback off their cost savings. For example using a pump from a coffee machine, or RC hobby servo motors to make valves instead of expensive custom parts.
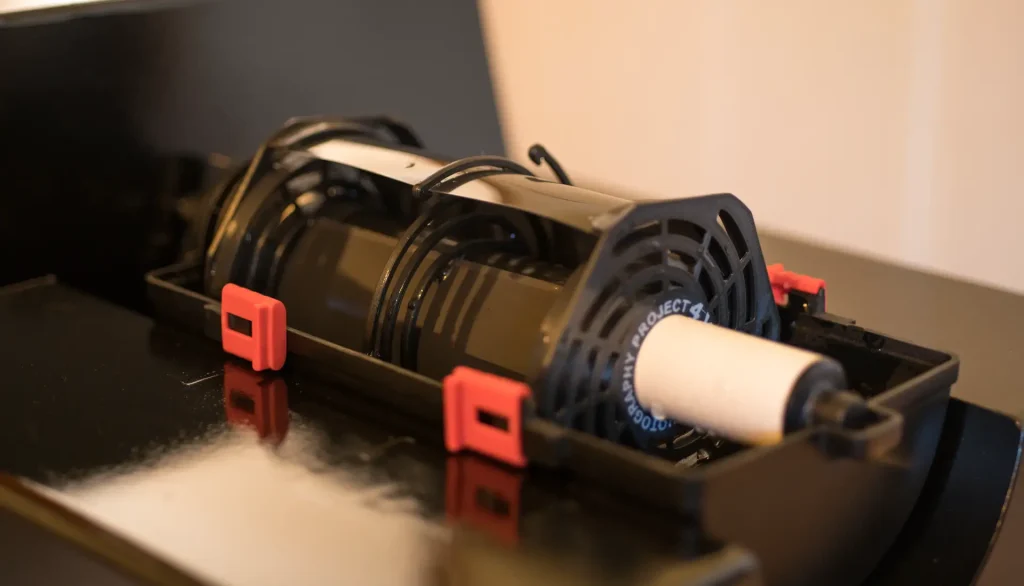
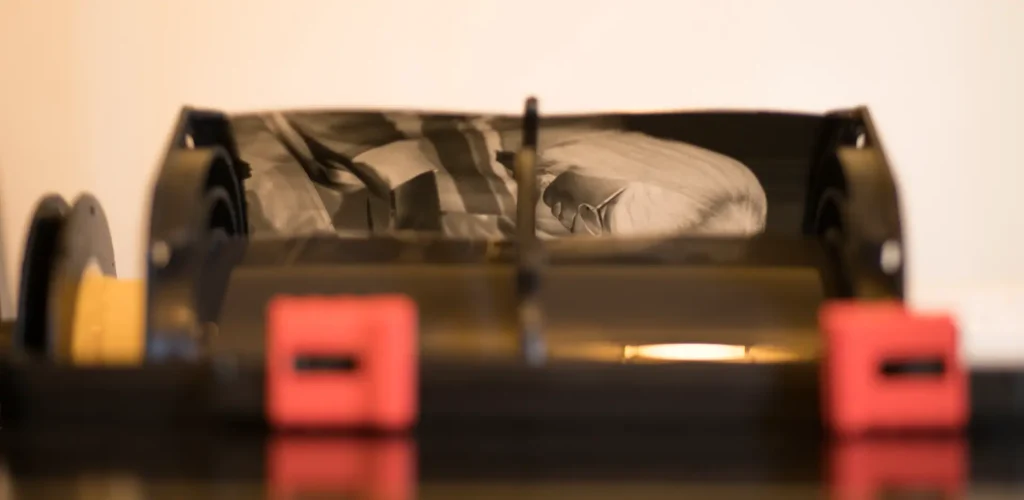
With a bit of effort and some clever design I’m hoping that I can end up with a machine both more capable but also cheaper and easier to use than anything comparable on the market today (or yet to be released that I’m aware of). A lot of people ask how much it’s going to cost and to a large extent that depends on demand, the more people want to buy them the cheaper they can be as my bargaining power with suppliers goes up. It’s currently looking like between $2.5k and $3k USD as a final retail price but I will be offering discounts for pre-orders, so there will be significant incentive to get in early.
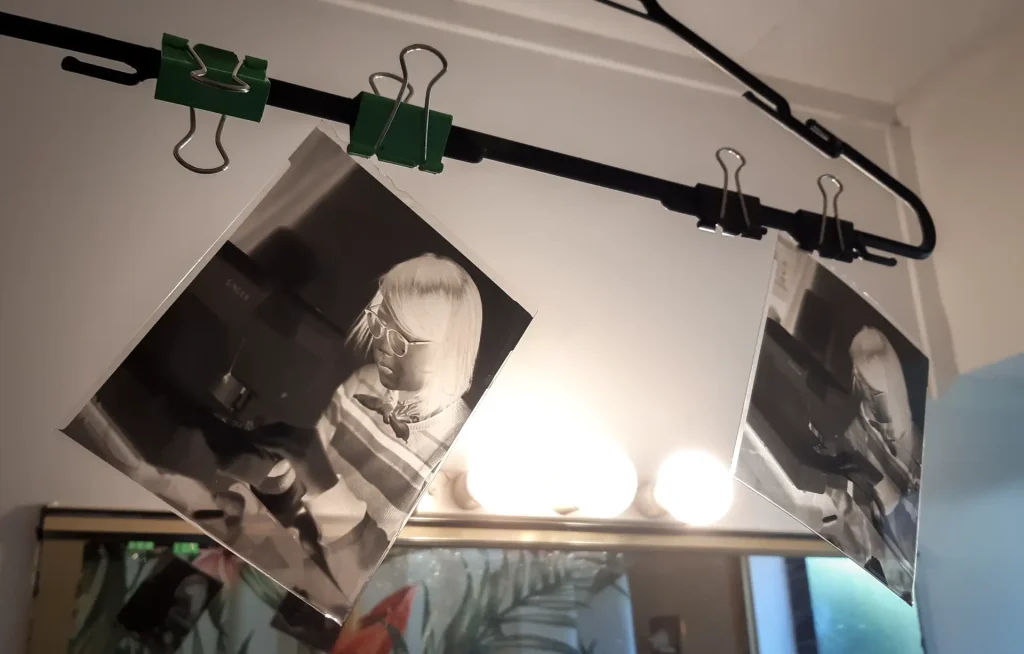
I’m hoping to start taking pre-orders via crowdfunding either at the end of this year or early 2021. I’m going to start with crowdfunding primarily as a way of gauging how much interest there is in the machine and to gather enough start-up capital to make larger quantity orders for cost-savings. I’m going to set a low ‘bar’ for success and if I can sell even 10 machines that will be enough for me to go ahead, so don’t worry too much about this project never taking off, I’m determined to deliver at the end of the day and I have a lot of experience making and delivering real hardware.
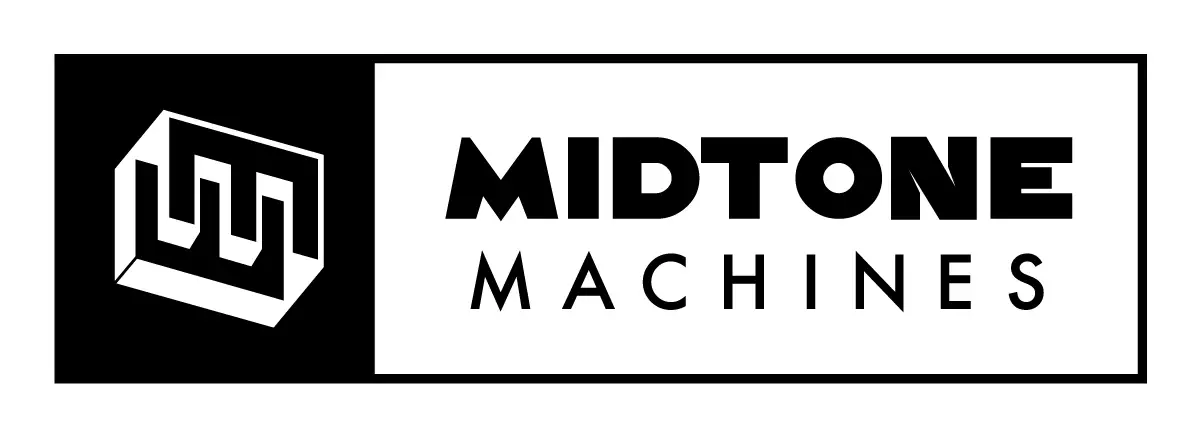
For more information and to get updates as they come I’d invite you to visit my website and sign up to the email list, or follow me on social media:
Website
Facebook
Instagram
Twitter
Share this post:
Comments
Niall on Midtone Machines – Introducing my Automatic Film Processor – By Andrew Burns
Comment posted: 26/11/2020
David on Midtone Machines – Introducing my Automatic Film Processor – By Andrew Burns
Comment posted: 26/11/2020
Michael Jardine on Midtone Machines – Introducing my Automatic Film Processor – By Andrew Burns
Comment posted: 26/11/2020
Perhaps we're spoilt in that the peak period for the quality of consumer appliances to the mass market (1980s/1990s I would argue) coincided with 35mm film being the popular medium, which is why we have such nice cameras to play with... but I digress.
Phil on Midtone Machines – Introducing my Automatic Film Processor – By Andrew Burns
Comment posted: 26/11/2020
Comment posted: 26/11/2020
Ted Smith on Midtone Machines – Introducing my Automatic Film Processor – By Andrew Burns
Comment posted: 27/11/2020
Comment posted: 27/11/2020
Comment posted: 27/11/2020
New Body Shells on Midtone Machines – Introducing my Automatic Film Processor – By Andrew Burns
Comment posted: 12/12/2020